Custom Logistics Management
System for a Leading Logistics Company
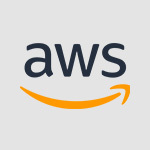
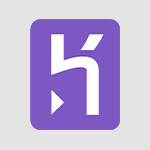
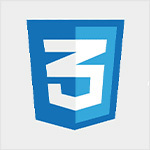
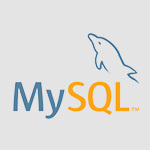
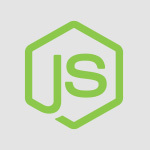
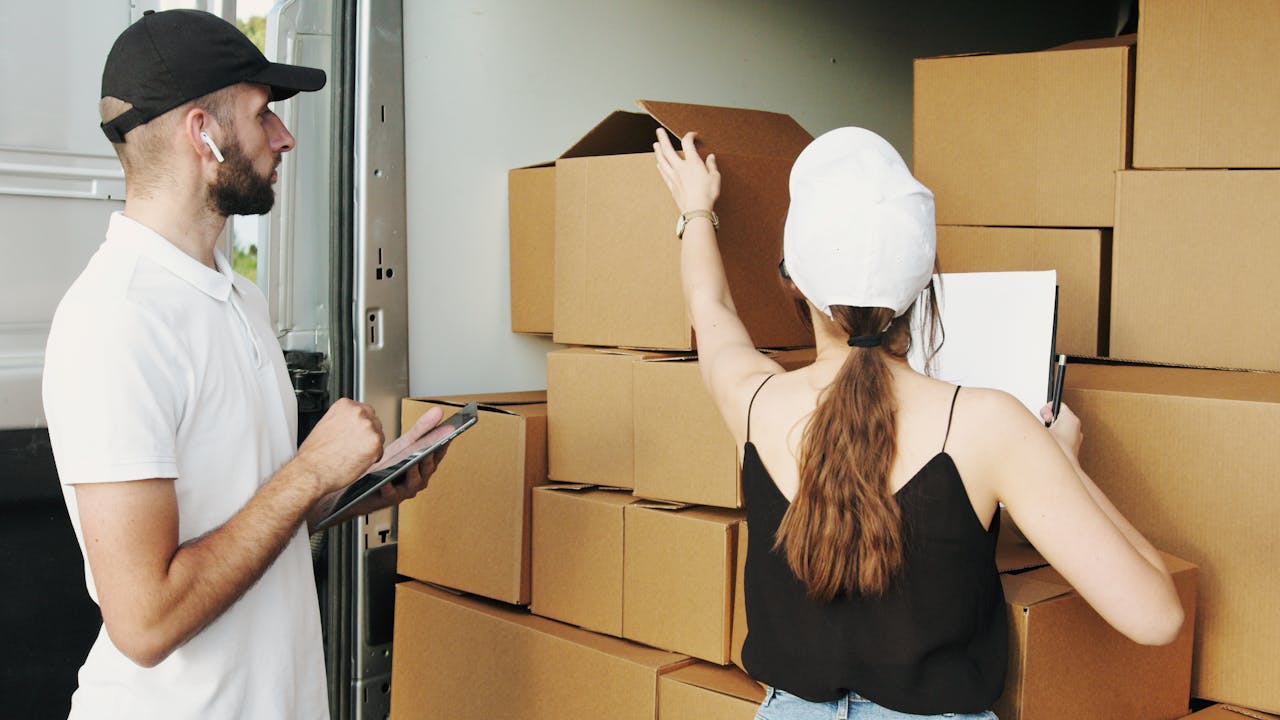
Overview
One such leading logistics company that takes care of a wide network for deliveries in both urban and rural areas was facing issues with route optimization, checking delivery progress, and operational transparency. Running a logistics operation with more than 3,000 vehicles in their fleet, the company required a scalable, automated and resource-efficient solution to optimize its logistics operations processes while also increasing delivery precision and client satisfaction. A specially tailored Logistics Management System (LMS) was successfully developed and deployed to overcome these hurdles while catering to business expansion as well.
PROBLEMS:
01 Inefficient Route Planning
Leading to routes with poor delivery paths from the start, wasting money on fuel, and having a gap between fleet capacity utilized.
02 Limited Real-Time Tracking
There was no single platform that enables them to track their fleet availability in real-time, adding difficulty for checking on delayed deliveries and how best to react.
03 Lack of Visibility on Delivery to the Customer
With no visibility of their delivery status, estimates or live tracking, customers were less trusting and satisfied.
04 High Return Rates
Regular delivery failures caused by wrong addresses, missed timelines or missing milestone confirmations (or the failure to induce the flows, as we had introduced above) increased operational expenditures and complexity.
05 Unable to Use Resources Efficiently
So, without information regarding the performance of vehicles and drivers, maintenance schedules or even delivery patterns, potential resources were left lying on the table while many incurred additional operational costs.
SOLUTIONS
Smart Routing Optimization
◉ Engineered a GPS based route optimization engine to calculate the optimal delivery process routes based on traffic and distance while also optimizing shipments by priority level.
◉ Allowed for dynamic re-routing in the event of road closures, changing traffic conditions or a need to get an urgent delivery request out on time.
Real-Time Fleet Tracking
◉ Fleet integration of IoT-enabled trackers for real-time location tracking.
◉ Built a unified dashboard for dispatchers to monitor vehicles, check delivery statuses and take proactive actions against delays.
Customer Delivery Portal
◉ Web and Mobile Portal Creation: Created a customer-facing web & mobile portal wherein customers can track their deliveries with estimated arrival times and real-time notifications are provided.
◉ Provided customers with the ability to self-serve their rescheduled delivery or address details.
Smart Delivery Verification
◉ Shifted to digital delivery confirmation tools, such as e-signatures, photo proof and QR code scans for accurate delivery confirmation.
◉ Implemented automatic alerts on failed deliveries with rescheduling options to minimize returns
Analytics and performance insights
◉ Constructed analytics dashboards for tracking delivery efficiency, driver performance and vehicle utilization
◉ Built-in predictive maintenance tools to keep a check on fleet health and minimize downtime
◉ Delivering actionable insights to optimize resource allocation, minimizing operational costs.
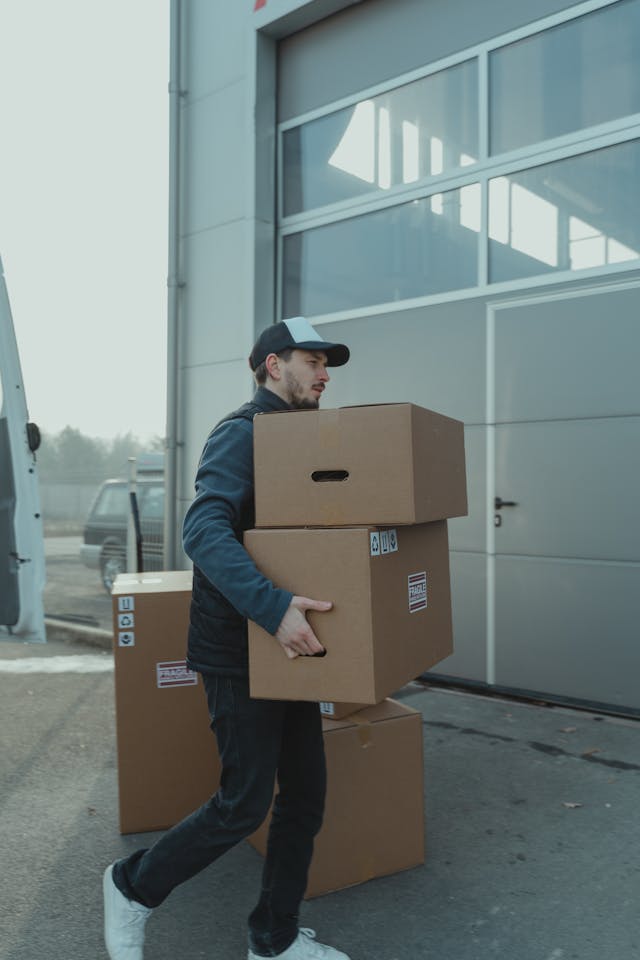
RESULTS
-
Increased Delivery Efficiency
Cut delivery time by 20%: Real-time traffic and order updates prevent delays and optimize routes.
Fleet Utilization Uplift Of 15%: Business hours for vehicles were correctly scheduled resulting in a much better utilization of vehicle capacity. -
Enhanced Real-Time Visibility
Real-time monitoring of the fleet allowed dispatchers to respond 25% faster when there were delays or incidents.
Live tracking & updates – had customers benefitting along with enhanced experience & trust. -
Reduced Delivery Failures
Enhanced accuracy of addresses and immediate notifications to customers led to a 30% decrease in unsuccessful deliveries.
Return logistics costs were minimized with automated rescheduling options -
Cost Savings
18% reduction in fuel costs was achieved through efficient routing and less time spent at idling.
Unplanned fleet downtime decreased by 40% owing to predictive maintenance, and as a result delivery performance was stable and reliable. -
Improved Customer Satisfaction
Fresh approach towards delivery uncertainties through delivery tracking, and alerts made customers more satisfied, with satisfaction curves moving up by 25%.
Conflicted deliveries caused by unresolved disputes and disputes arose; this in turn also improved the reliability of the service.